Standing at 78 meters tall, the Museum of the Future (MOTF) is far from reaching Dubai’s famous skyline, which features skyscrapers like the unparalleled Burj Khalifa – the world’s tallest tower.
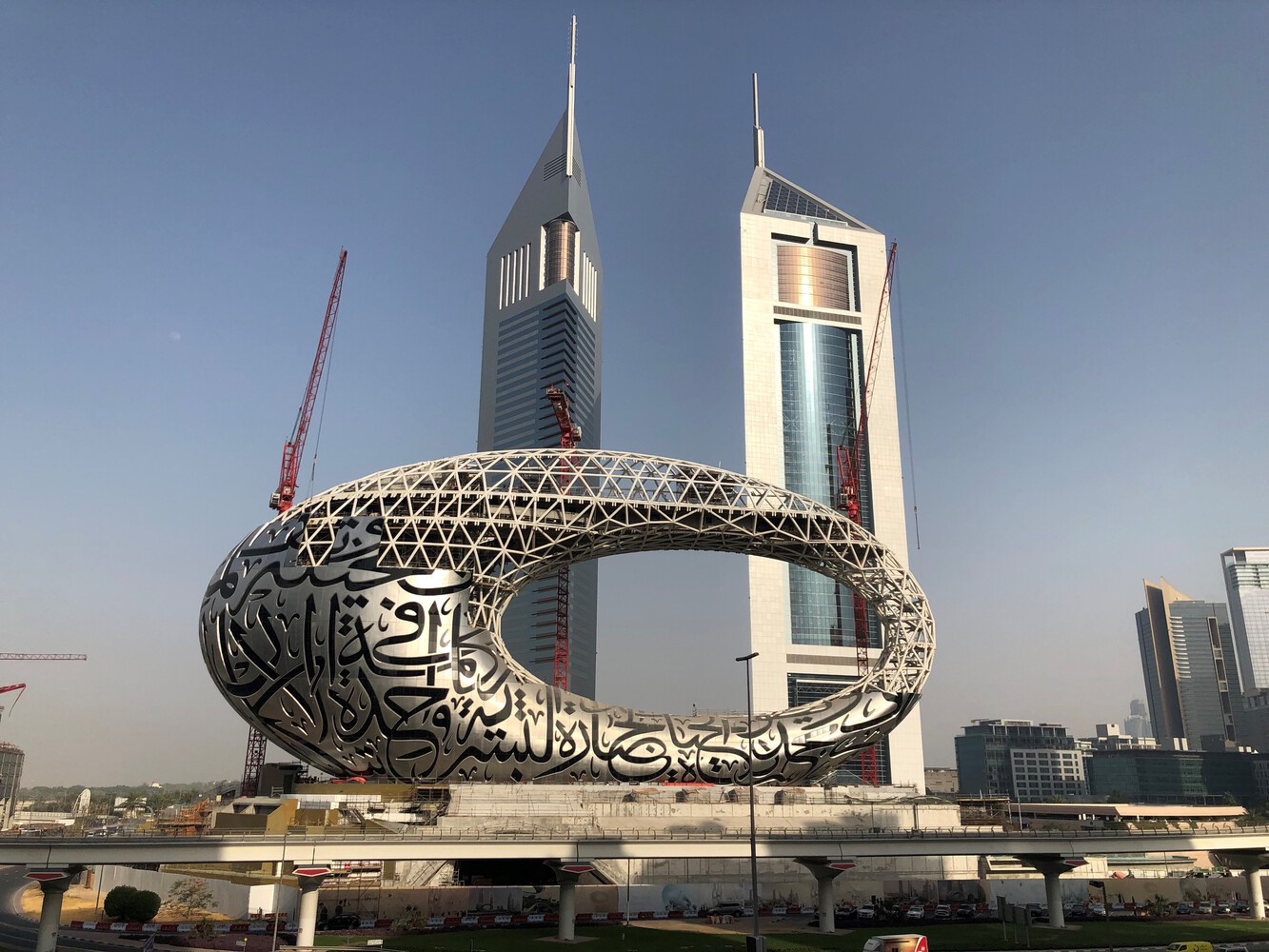
However, with its bold shape and striking façade illuminated by more than 14,000 meters of Arabic calligraphy, it certainly succeeds in taking its place among the city’s most iconic buildings. The award-winning project by Killa Design and Buro Happold, described by many as ‘the most beautiful building in the world’, opened in February of 2022 in Dubai’s Financial District. In a total built-up area of 30,000 sqm, it accommodates exhibition spaces for innovative ideologies, services, and products, as well as theatre spaces, a laboratory, and a research centre.
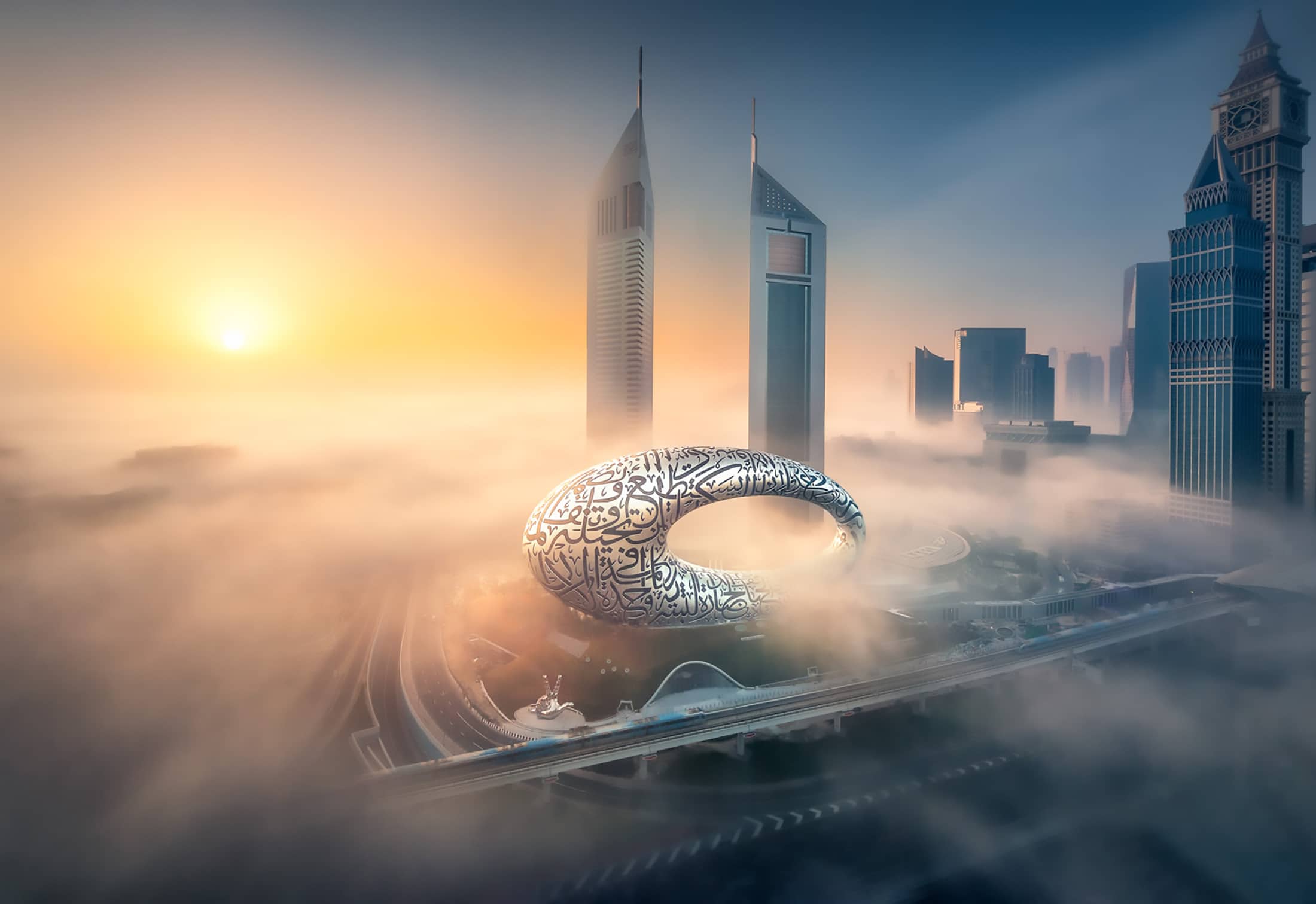
Symbolizing Arab heritage and future progress, MOTF is comprised of three main parts: a green hill, the building, and the void. The green hill represents the earth – with its roots in place –, time and history. It also serves to unobtrusively elevate the museum above the adjacent metro line and create an elevated park. Likewise, the torus-shaped structure symbolizes mankind’s ability to innovate and push the limits of modern engineering and construction. The elliptical void, on the other hand, is an expression of ‘the unknown’ that seeks to inspire today’s creators to face humanity’s unwritten future.
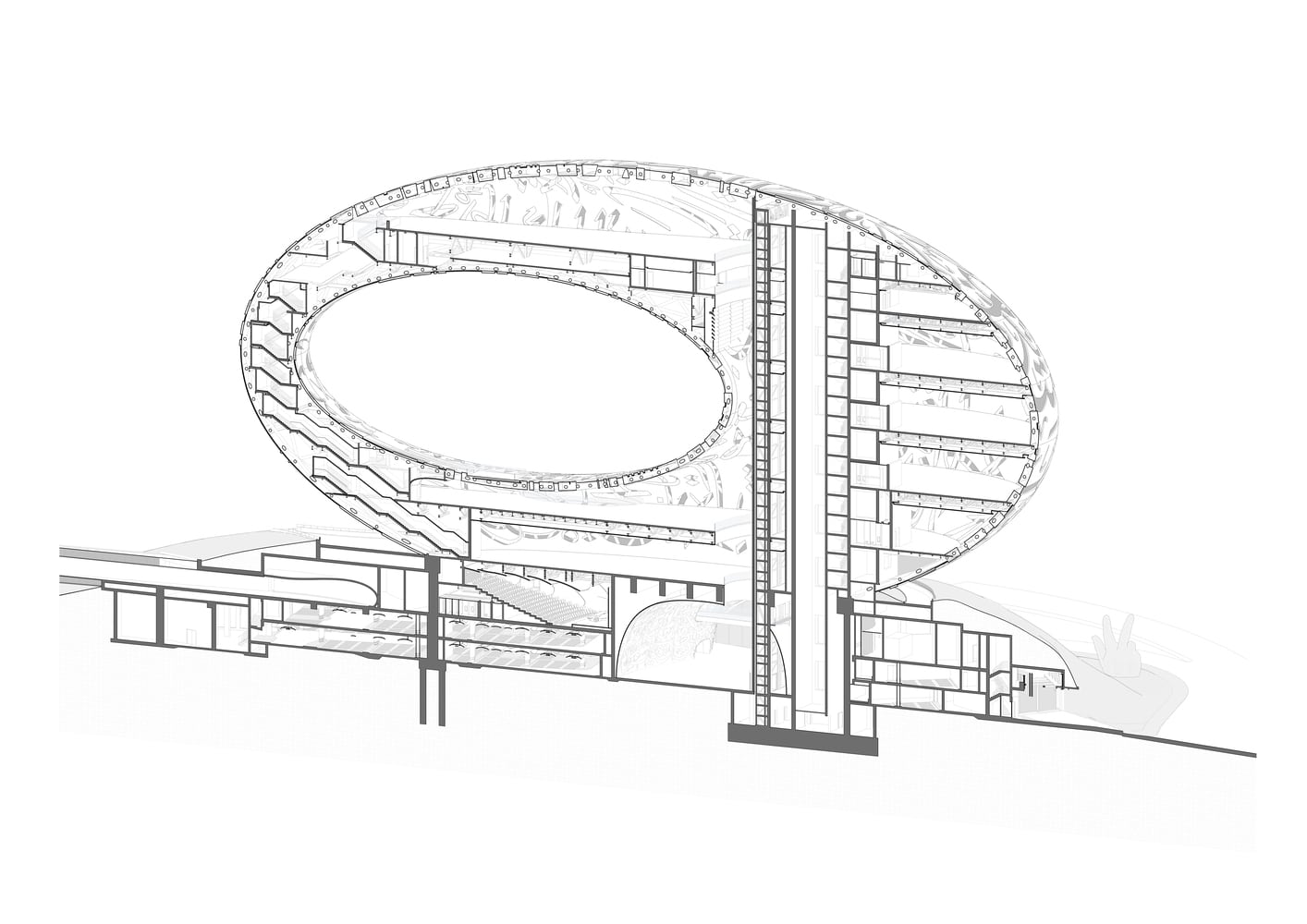
With its magnitude, eye-catching form and extremely intricate design, the architectural and engineering marvel is one of the most advanced structures ever built. As a result, it called for a series of groundbreaking technologies to approach complex design challenges and bring the vision to life. To find out more about these technologies, we spoke with Shaun Killa and Pippa Tucker from Killa Design, the architecture firm behind the monumental building.
The Museum of the Future has been one of the most stimulating projects I’ve designed as it is a highly public cultural building, hyper unique in its form and technically complex in its execution. – Shaun Killa, co-founder of Killa Design and chief architect of MOTF
Challenges behind the revolutionary design
Many of the challenges encountered by architects and engineers arose from the complexity of the diagrid and façade. To overcome them, the design process required a combination of advanced materials and the latest technologies in 3D modelling software, collaborative design, and parametric construction. These digital tools were ultimately pivotal to the success of the project, which wouldn’t have been possible otherwise.
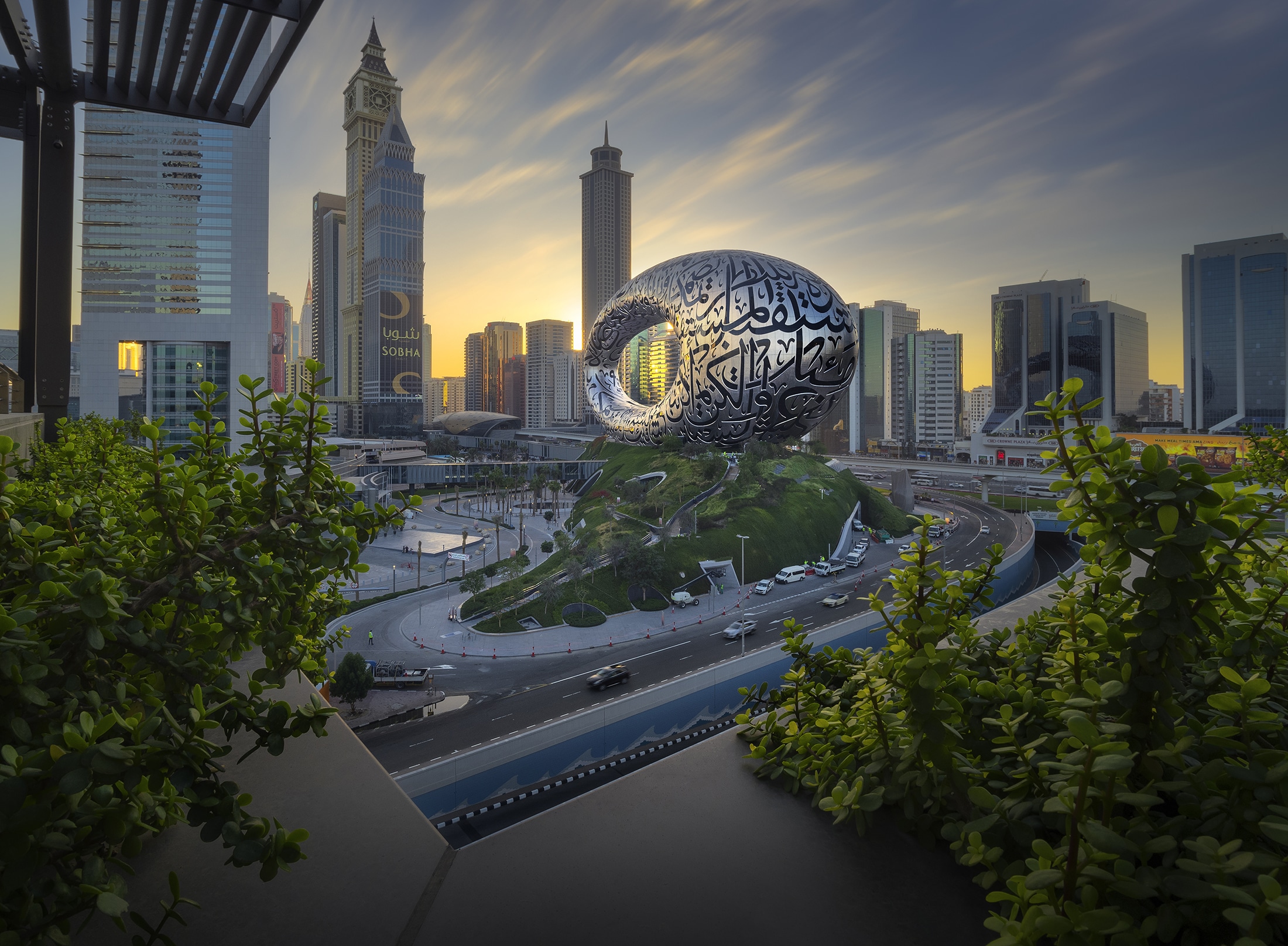
As Shaun and Pippa shared with us, one of the most difficult features to construct was the building’s curved façade, consisting of 1,024 glass-reinforced plastic and stainless-steel panels. Integrating the moulded-in Arabic calligraphy in distinct 3D shapes, the carved panels play a fundamental role. During the day, they function as windows that cast natural light through the column-free interior; during the night, they illuminate the city with LED lighting. And with a depth of 1.3 meters, the windows are wide enough for visitors to stand inside in what functions as a permanent exhibition space. However, the team had to overcome multiple complexities to achieve this end result.
A major challenge in the design of the Museum of the Future was the incorporation of the calligraphy windows into the parametrically optimized torus form, inclusive of the avoidance of the steel diagrid structural nodes through the calligraphy, all of which took over a year to design. – Shaun Killa, co-founder of Killa Design and chief architect of MOTF
Other significant challenges related to execution included “coordination of more than 1,000 unique structural nodes and their base connections, as well as clash avoidance with secondary support steel work, fit out and MEP (mechanical, electrical and plumbing).”
Innovative design principles
To address all of these complexities, the project adopted numerous innovative design principles regarding construction technologies and materials. This involved, for example, developing parametric design tools with growth algorithms “to digitally optimize the efficiency of the primary structural diagrid, façade, and the glazing elements.” The software included Revit with Dynamo and Rhino with Grasshopper. Likewise, the use of BIM was pivotal during the process, creating a precise digital model with multi-disciplinary collaboration. It was also used to produce all the drawings and for Virtual Reality clash detection, deflection tolerances and onsite real-time building sequences.
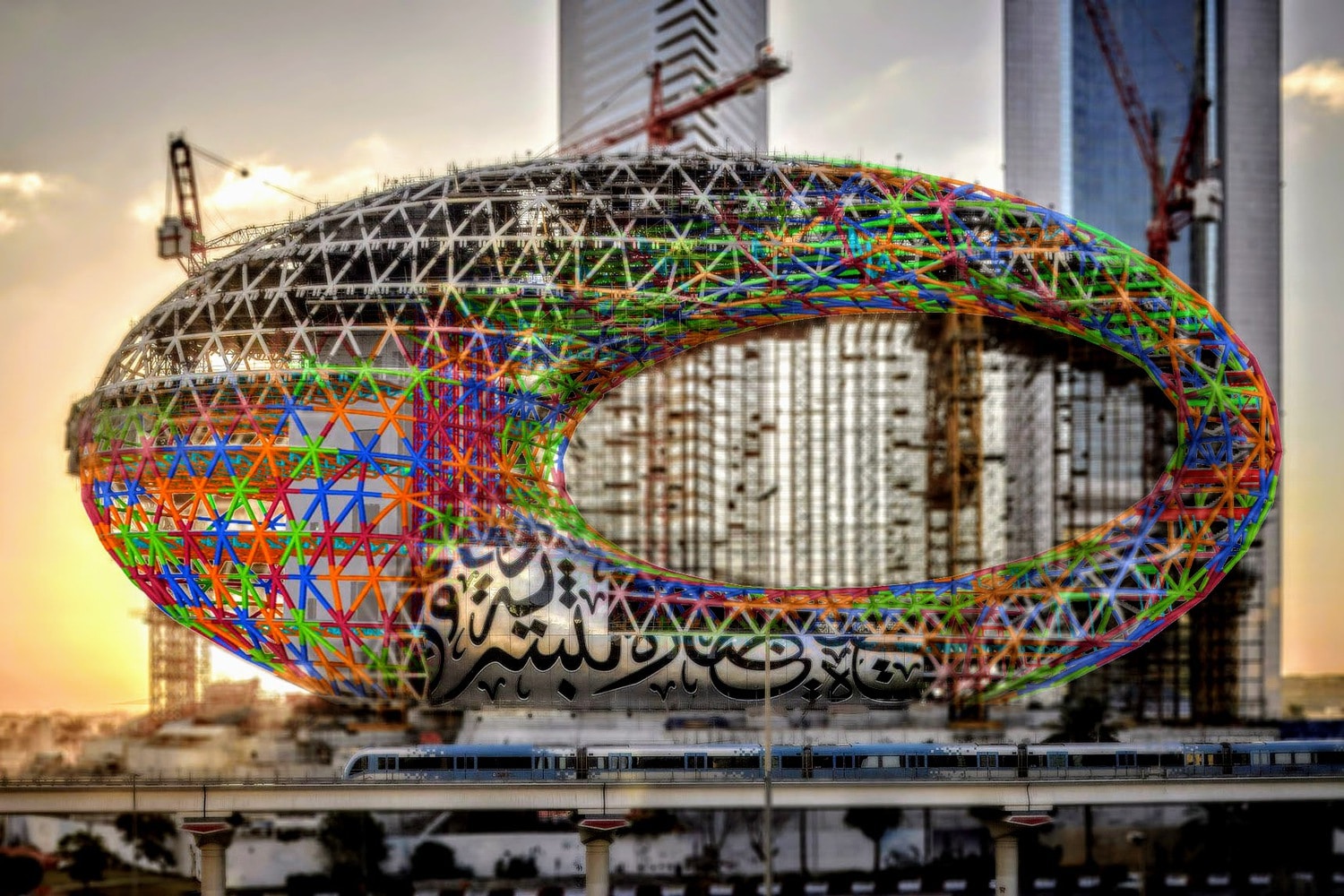
Tekla Structures, a structural BIM software developed by Trimble, was utilized considering the museum’s unconventional geometry and massive amounts of data. Besides providing powerful 3D modeling capabilities, the technology was extensively used to identify clashes with other trades like MEP, roofing and façade contractors. Furthermore, the solution enhanced and simplified design details, enabled smoother workflows and delivered the intricate interface requirements during the designing, fabricating and coordinating phases of the project. It also allowed different actors to explore and develop routines to do modeling and detailing accurately in a short period of time. Overall, the innovative use of each digital design tool resulted in maximum optimization.
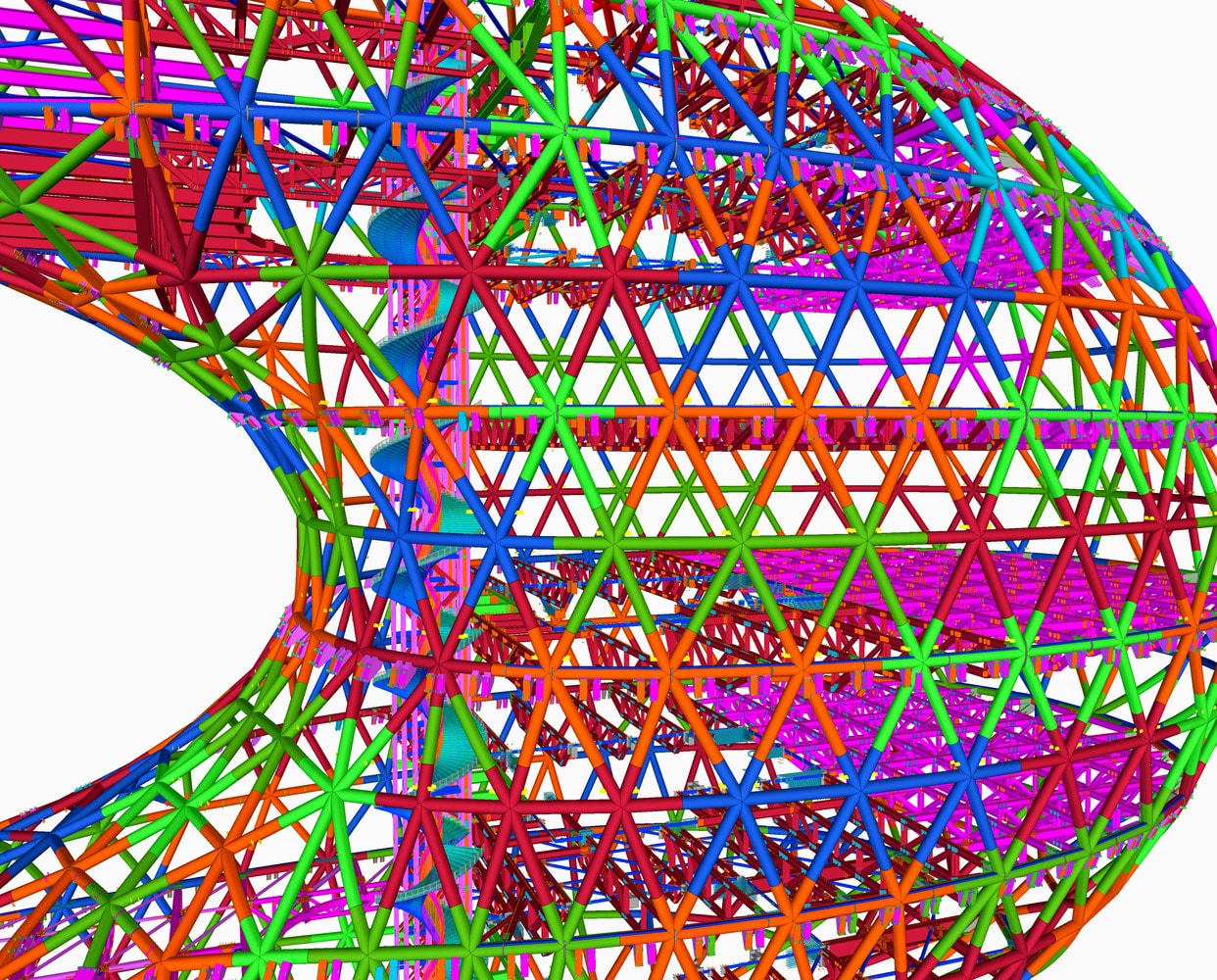
The computer aided design for the Museum of the Future was unique in respect to its algorithms and the scripting that was required to design an optimized form and structural system. – Killa Design
High-tech procedures, like aviation software and automated robotic arms, were particularly needed to put together the calligraphy panels covering the exterior. First, 3D modeling software was used to set the calligraphy onto the building’s surface and to guarantee that the 1,000 steel diagrid nodes were avoided in the center of the windows. For their construction, the process involved “CNC robotic technology and cutting-edge moulding and processing systems, which required a 16-step process to produce.” And to accurately place the panels in the structure – and ensure their dynamic movement without any distortion –, the team utilized multi-layered laser positioning systems, which were also used for the precise placement of the steel diagrid.
Technology in favor of wellbeing and sustainability
As Shaun Killa claims, sustainability was the main motivation in the design, which was also addressed through advanced technologies: “The aspiration was to make the design, the fabrication and its operational resources as sustainable as possible using the highest innovative technologies.” This involved developing a 3D energy model, low-energy and low-water engineering solutions, recovery strategies for energy and water, passive solar design, air quality filtering systems and integrated renewables from a nearby solar farm located on car park building rooftops. Altogether, this contributed to a 45% reduction in water use and total energy savings of 25%. The result is a low carbon building with LEED Platinum certification that aims to set the example for all future buildings in the UAE.
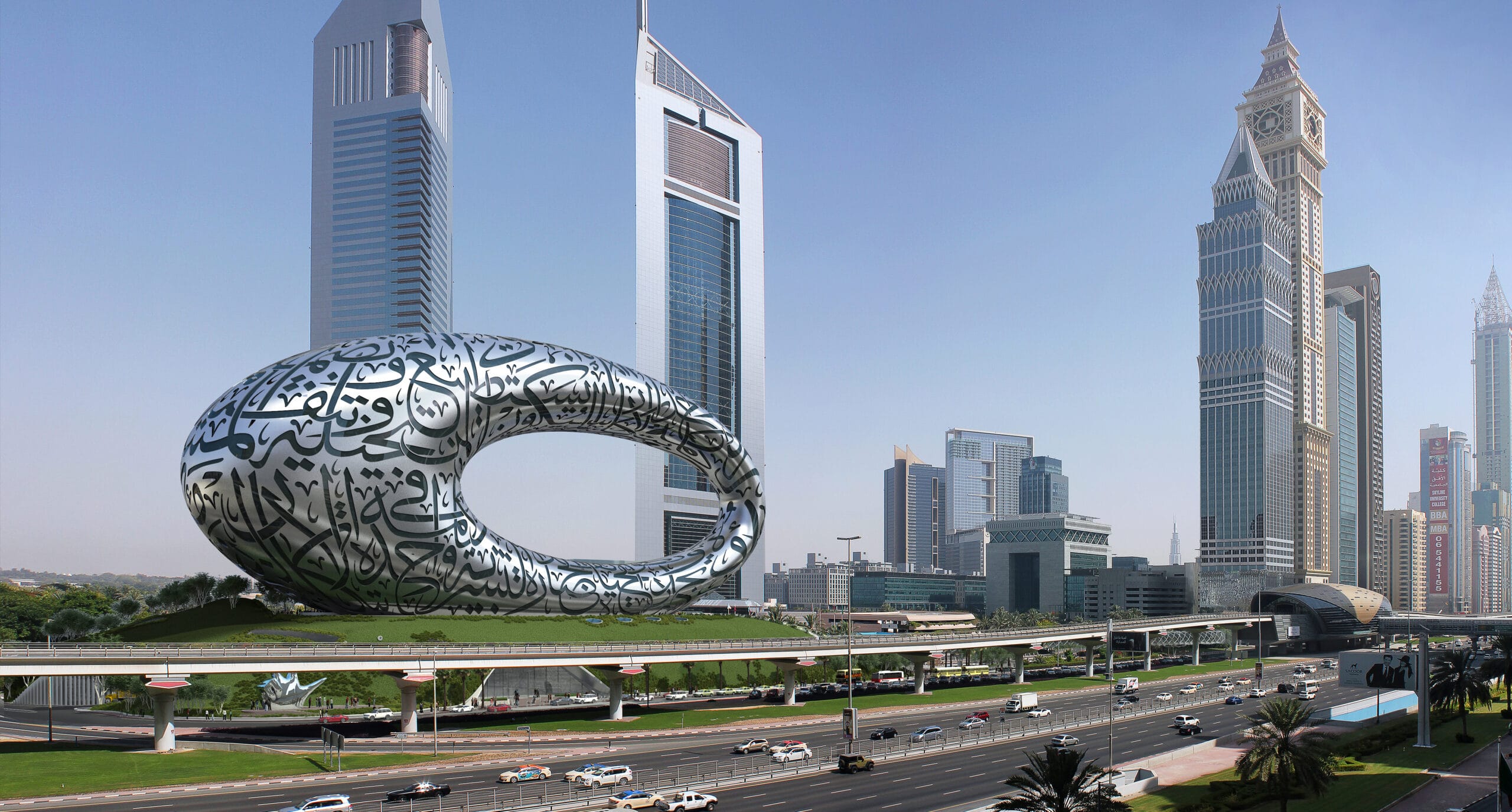
The Museum of the Future is an architectural and engineering masterpiece that takes a groundbreaking approach to what it means to be a museum. Without a doubt, a great part of its success lies in its multi-disciplinary collaboration and the innovative use of the latest technologies; from robotics to parametric design, from CNC to aviation software. Pushing the limits of innovation, the iconic landmark paves the way towards a promising future, one where technology takes part of the built environment in favor of creativity, wellbeing and sustainability.